The Oxford Applied Research mini e-beam evaporators are employed to deposit ultra-pure films of materials. The deposition rate is highly controllable, allowing the instruments to be employed in Surface Science or thin-film applications. Full control from <0.1Å/min to >50Å/min is achieved for many materials. It is also possible to co-evaporate up to four materials with independent regulation of the deposition rate from a single power supply (pictured below).
The evaporators all share a consistent design philosophy, which focuses on the most important features for UHV deposition: low contamination, low particulate generation and high reliability. Our evaporators have no moving parts, allowing direct water-cooling of the target holder which in turn leads to extremely efficient heat transfer.
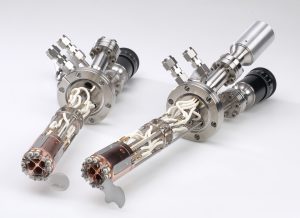
During tungsten evaporation at >3000oC, for example, the temperature of structural components and adjacent pockets remains below 35oC in our four-pocket device. This eliminates the temperature rise and subsequent contamination inherent in inefficiently-cooled competitive instruments. Furthermore there is no risk of particulate generation, bellows failure or internal seizure of moving parts.
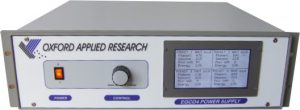
Principle of Operation
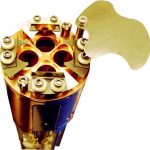
The evaporant can be either a rod or contained within a crucible. The rod/crucible is held at high voltage during operation, which acts to draw an electron current from a nearby hot filament. The energetic impact of the electron beam raises the temperature of the evaporant, creating a hot tip on the rod or a heated ‘oven’ in the case of the crucible. With a sufficiently elevated temperature, the material will begin to evaporate. In four-pocket devices, each pocket is equipped with an independently regulated filament and provided with cross-contamination shields.
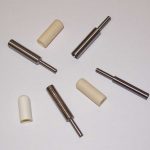
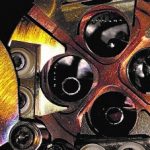
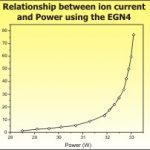
Ion Current Monitoring
An intrinsic part of the evaporation process results in a small fraction of the vapour being in an ionised state. This phenomenon can be harnessed to determine the deposition rate without recourse to film thickness monitors during evaporation. All evaporators are equipped with ion flux monitoring which not only measure the current in the beam, but also extract the vast majority of the ions, leaving the beam predominantly neutral.
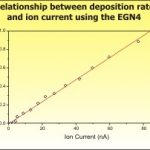
Accessories
Uniformity
The central deposition profile from the source is essentially identical to the cosine2 distribution from a point source. At 100mm from the source exit the evaporant beam can cover a 20×20mm sample with a uniformity better than 98%.
Software control (EGCO4) – Optional hardware additions to the power supply allow control from WindowsTM-based software. The software package allows control of key parameters inherent to the operation, as well as simulating control of indirectly affected parameters such as flux. This greatly simplifies practical operation for the user. The latest generation of software communicates with the power supply via a standard USB (universal serial bus) interface. |
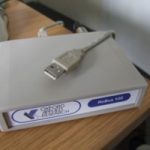
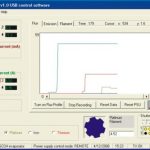
Shutter – All evaporators can be equipped with an integral shutter. The shutter on the EGCO4 allows several combinations of pockets to be selectively opened. Crucibles and liners – The evaporators can be fitted interchangeably with crucibles or rods. Crucibles are suitable for use with insulators, materials which require an evaporation temperature significantly higher than the melting point or which have a very high thermal conductivity. Liners are recommended where metals are prone to alloying. Hardware flux control (EGN1 and EGN4) – The evaporator power supplies can be externally or internally controlled by optional hardware designed to maintain a constant deposition rate. The flux-controller hardware uses the ion current measured from the flux monitoring plates in a feedback loop to regulate the power applied to the evaporant. |
Calibration of EGN4 evaporator using STM: Silicon at low deposition rates |
162mm3 crucible filled with pieces of intrinsic Si wafer. Substrate is clean Si(100)-2×1 Sample-source distance: 100mm Power: 40W Flux: 4nA Pressure during deposition: 3×10-10mbar
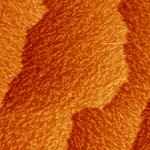
200X200nm
The Si coverage is calculated to be 0.2ML from these images. A 4nA flux therefore corresponds to a rate of 0.8ML/min (0.11nm/min) Data provided by Dr.Matt Butcher University of New South Wales, Australia
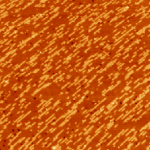
100X100nm
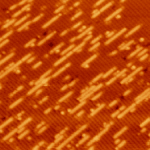
35X35nm
Calibration of other elements using a quartz crystal monitor and flux monitoring
The following data was taken using an EGN4 and it can also be applied to the EGCO4. The graphs show the power through the rod or crucible vs the deposition rate (at a distance of 100mm) and the flux (ion current).
1. Evaporation of materials from crucibles Materials with low evaporation temperatures or insulating properties should ideally be deposited from crucibles. The evaporator should be positioned at an angle of at least 30o to the horizontal so that the molten material does not flow out. As the material is in different positions within the crucible it is advisable to slowly outgas and heat the material. Once a small flux is observed the power (or filament current for the EGCO4) should be increased in very small amounts to prevent sudden bursts out of the crucible. For material in crucibles there may be variations in the power required to give a particular flux. This is due to amount and position of material in the crucible. For the EGCO4 the exact ratio of filament current to emission current can also vary from pocket to pocket due to the material, the position of the material in the crucible, and the position of the crucible within the pocket. The deposition rate is determined using a quartz crystal monitor at a distance of ~100mm from the end of the evaporator.
2. Evaporation of material in rod form 2mm rods are used. For the EGCO4 the ratio of the filament current to the power will vary from pocket to pocket depending on the material and the size of the rod. As the rod becomes shorter, due to evaporation, the filament current will be required to be higher to maintain the flux. When the rod becomes very short, and closer to the cold hearth, it may also be necessary to increase the power to maintain the flux.
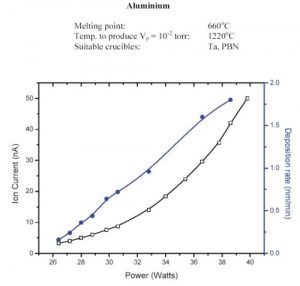
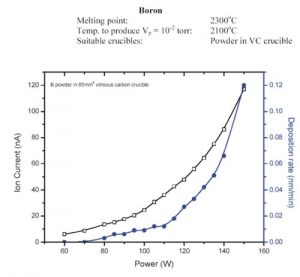
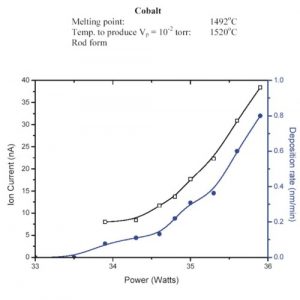
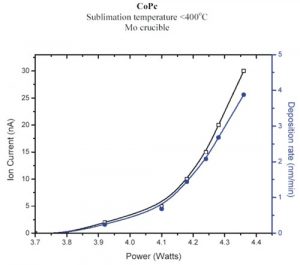
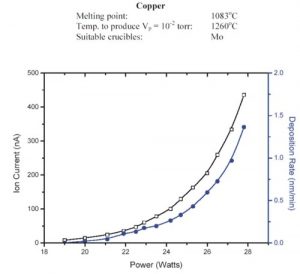
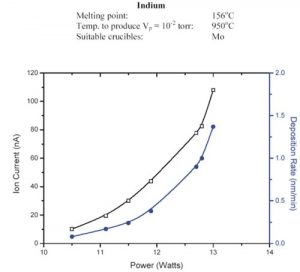
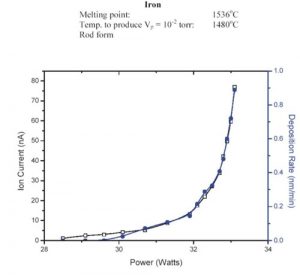
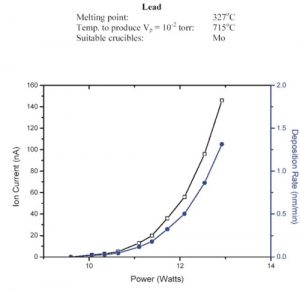
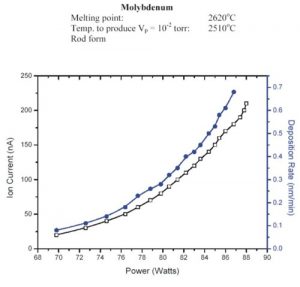
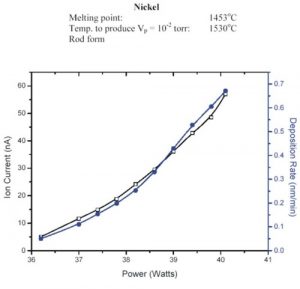
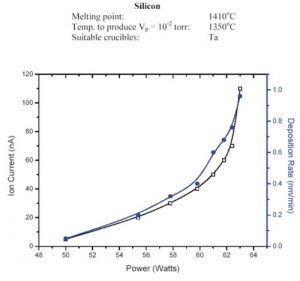
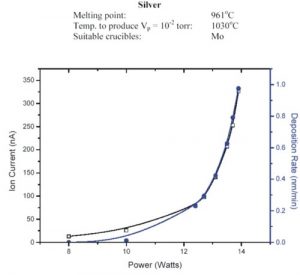
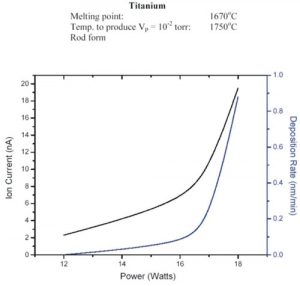
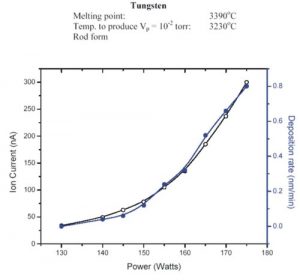
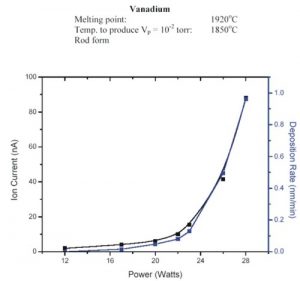
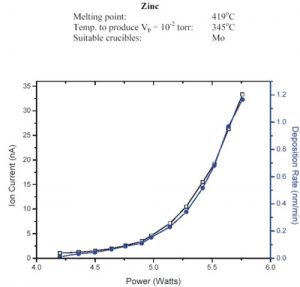
Click here for Publications.
Download the brochure in PDF format : EG Series